Top Techniques for Efficient Aluminum Casting Process Unveiled
By:Admin
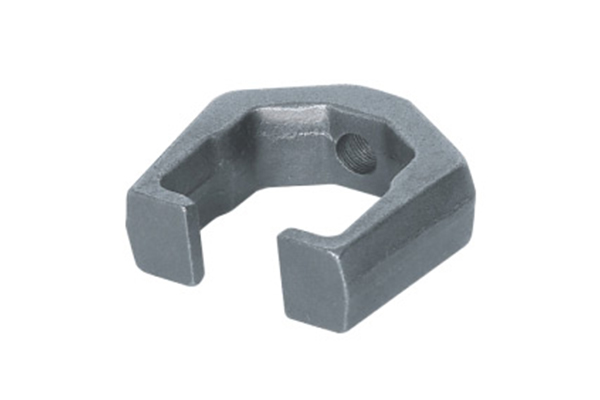
Introduction:
In an era driven by technological advancements, the manufacturing industry is witnessing a groundbreaking innovation: Aluminum Casting. The technique of casting aluminum has caught the attention of various industries owing to its strength, flexibility, and cost-effectiveness. In this news piece, we explore how one company, with its expertise in Aluminum Casting, is transforming the manufacturing landscape.
Company Introduction: [Remove brand name]
The company at the forefront of this aluminum casting revolution is a leading manufacturer with unparalleled expertise in the field. Their extensive experience and dedication to excellence have earned them a prominent position within the manufacturing industry. Committed to delivering outstanding results, this company has developed state-of-the-art facilities, advanced equipment, and a team of highly skilled professionals who share a passion for innovation.
Breaking Down Aluminum Casting:
Aluminum casting is a process that involves making three-dimensional objects by pouring molten aluminum into a mold, enabling the creation of complex and intricately designed components. The versatility of this method allows manufacturers to produce parts of different shapes, sizes, and designs, catering to various industries such as automotive, aerospace, construction, and electronics.
Revolutionizing Manufacturing Processes:
1. Lightweight Advantages:
One significant advantage of aluminum casting lies in the lightweight nature of the material itself. As a result, industries such as automotive and aerospace are increasingly opting for aluminum components over traditional materials like steel. The reduction in weight contributes not only to improved fuel efficiency but also to enhanced performance and maneuverability of vehicles. Moreover, lightweight aluminum components reduce the overall carbon footprint, promoting sustainability within the industry.
2. Strength and Durability:
Aluminum casting offers exceptional strength and durability. The unique characteristics of aluminum make it an ideal choice for parts subjected to high stress, heat, or corrosive environments. This advantage translates into longer lifespan, minimized maintenance costs, and increased reliability of the final products.
3. Cost-Effective Solutions:
By utilizing aluminum casting, manufacturers can achieve significant cost savings. Aluminum, being abundant and readily available, is a cost-effective material option compared to other metals. The simplicity of the casting process also contributes to reduced production time and cost, making it an economically viable solution for a wide range of industries.
4. Design Freedom:
Aluminum casting provides designers with unmatched freedom to create intricate and complex shapes. The molten aluminum can be easily customized and cast into various molds, allowing manufacturers to meet their clients' specific requirements with ease. This advantage enables the production of highly customized components that enhance product aesthetics and functionality.
Conclusion:
The advent of aluminum casting has undoubtedly revolutionized the manufacturing industry, offering numerous benefits such as lightweight construction, superior strength, cost-effectiveness, and design freedom. As companies continue to harness the potential of this technique, we can expect to witness groundbreaking advancements in various sectors. With its extensive expertise, state-of-the-art facilities, and dedicated team, the company stands at the forefront of this aluminum casting revolution, paving the way for a future driven by innovation, reliability, and sustainability in manufacturing.
Company News & Blog
New Developments in Cold Forging Die Technology: Exploring Advancements in Metal Forming Processes
Title: Advancements in Cold Forging Die Technology Enhance Manufacturing Efficiency Introduction:In a world where precision and efficiency are paramount, companies across various sectors are continually seeking advanced techniques and tools to optimize their manufacturing processes. Cold forging, a metalworking technique known for its ability to produce high-quality components with exceptional strength and precision, has witnessed a significant breakthrough with the introduction of a cutting-edge Cold Forging Die by {} (company name).Cold Forging Die Technology:The recently developed Cold Forging Die by {} is revolutionizing the manufacturing industry. With its state-of-the-art design and innovative features, this tool ensures improved production efficiencies, reduced costs, and enhanced product quality. The cold forging process involves shaping a metallic workpiece by applying immense pressure at ambient temperatures. The Cold Forging Die, an essential component in this process, plays a critical role in determining the accuracy, productivity, and longevity of the finished products.By removing the inherent limitations of traditional forging dies, the advanced technology employed in the Cold Forging Die by {} delivers unparalleled precision and durability. The die's design incorporates cutting-edge materials, surface treatments, and advanced coatings that significantly reduce wear and tear, thereby extending its lifespan and minimizing downtime requirements for die replacement.Key Features and Benefits:1. Enhanced Durability: The Cold Forging Die by {} boasts exceptional durability due to the utilization of premium quality materials and specialized surface treatments. This ensures the die can withstand high-pressure forces, reducing the need for frequent replacements and minimizing associated costs.2. Improved Precision: With stringent accuracy requirements in various industries, this advanced die technology guarantees precise shaping and dimensional stability for the forged components. The die's design incorporates optimal geometries and surface finishes, resulting in flawless product formation and increased reliability.3. Customization: {} understands the diverse requirements of different industries and offers a range of customized Cold Forging Dies. This flexibility allows manufacturers to produce components with complex shapes, enhancing their product portfolio and expanding market opportunities.4. Cost Efficiency: By optimizing the cold forging process, this advanced die technology increases production efficiency, leading to reduced lead times and enhanced cost-effectiveness. The die's superior performance minimizes material waste during manufacturing, ensuring maximum yield and reducing overall production costs.5. Versatility: {} Cold Forging Dies efficiently cater to a wide array of applications across industries like automotive, electronics, construction, and machinery. Whether it's forming intricate slots, threads, or intricate shapes, these dies offer versatility and reliability to meet the diverse needs of manufacturers.Company Overview:With a vision to revolutionize the metalworking industry, {} (company name) has been at the forefront of innovative manufacturing solutions for over two decades. The company's commitment to research and development, coupled with its customer-centric approach, has enabled them to introduce groundbreaking tools such as the Cold Forging Die.As an industry leader, {} constantly strives for excellence and has established a strong reputation for delivering world-class precision tools. Their team of experienced engineers and technicians collaborate closely with clients to understand their specific requirements and develop tailored solutions.Conclusion:The introduction of the cutting-edge Cold Forging Die by {} marks a significant milestone in the manufacturing industry. As companies strive for greater efficiency, precision, and cost-effectiveness, this advanced die technology offers unparalleled benefits. With its enhanced durability, improved precision, and customization options, {} Cold Forging Dies are set to revolutionize the cold forging process, attracting manufacturers across various industries. Expect notable advancements and further innovation from {} as they continue to shape the future of the metalworking industry.
Quality Hand Forged Iron Coat Hooks: A Must-Have for Every Home!
Hand Forged Iron Coat Hooks: The Perfect Combination of Style and FunctionCoat hooks serve an essential purpose in our everyday lives, offering a convenient solution for organizing our outerwear. While functionality is undoubtedly important, it does not mean compromising on style. Hand Forged Iron Coat Hooks, an innovative product (brand name needed), is taking the market by storm with its unique blend of functionality and aesthetics.Hand Forged Iron Coat Hooks are meticulously crafted using traditional blacksmithing techniques. The company behind this exquisite creation, which is committed to bringing art into everyday life, has been a prominent figure in the industry for years.The manufacturing process begins with skilled craftsmen who heat iron rods in a forge until they are malleable enough to be shaped into the desired form. These craftsmen skillfully transform these rods into beautifully designed hooks by carefully hammering, twisting, and welding each piece with the utmost care and precision.The result is an astonishing range of hand forged iron coat hooks that are not only practical but also a true work of art. Each hook is unique, showcasing the individuality and creativity of the craftsmen. The attention to detail is evident in every curve and twist, creating a visually appealing element for any living space.But Hand Forged Iron Coat Hooks, however visually stunning, are not just for decorative purposes. Coming in a variety of sizes and styles, they offer a practical storage solution for your coats, hats, scarves, and other items that need to be easily accessible. The sturdy iron construction ensures they can withstand the weight of heavy winter coats, while still maintaining their timeless aesthetic appeal.Additionally, Hand Forged Iron Coat Hooks also offer versatility in their installation options. Whether you prefer a traditional wall-mounted design or wish to create a unique display using a stylish coat rack, these hooks can be easily adapted to suit your individual needs and design preferences.Moreover, these hooks are not limited to home use alone. The durability and unique design make them a perfect addition to commercial spaces such as hotels, restaurants, and boutiques. They add a touch of elegance and sophistication while providing customers with a functional and convenient storage option.When compared to mass-produced hooks, Hand Forged Iron Coat Hooks stand out for their superior quality and craftsmanship. Each hook is carefully inspected to ensure it meets the company's high standards before reaching the customers' hands. The attention to detail and commitment to excellence set these hooks apart from their competitors.In addition to their exceptional products, the company follows environmentally friendly practices throughout their manufacturing process. By utilizing traditional blacksmithing techniques, they minimize the negative impact on the environment commonly associated with mass production.Hand Forged Iron Coat Hooks have quickly gained popularity among interior designers and homeowners alike. Their ability to effortlessly blend into various interior styles, whether it be rustic, traditional, or contemporary, has made them an essential element in creating visually appealing and functional spaces.In conclusion, Hand Forged Iron Coat Hooks have emerged as a leading choice for those seeking a perfect combination of functionality and style. With their unmatched craftsmanship, attention to detail, and commitment to quality, these hooks are sure to be a valuable addition to any living or commercial space. By choosing Hand Forged Iron Coat Hooks, you not only invest in a practical storage solution but also add a touch of timeless elegance and beauty to your everyday surroundings.
The Ultimate Guide to Flange Forging Process: Everything You Need to Know
Title: Innovating Flange Forging Process to Enhance Manufacturing EfficiencyIntroduction:In the ever-evolving field of manufacturing, companies are constantly seeking innovative solutions to improve production processes and meet the growing demand for quality products. One such company, with a rich history of expertise in the industry, has successfully developed an advanced flange forging process that aims to revolutionize manufacturing efficiency. By combining cutting-edge technology, extensive research, and strategic partnerships, this company is poised to redefine the standards of flange production.Breaking News: Advancements in Flange Forging Process{Company Name}, a prominent player in the manufacturing sector, has recently introduced a game-changing flange forging process in response to the market's increasing demand for high-quality products. This innovative technique optimizes the production process, thereby enhancing efficiency and ensuring superior product performance.The conventional methods of manufacturing flanges are often time-consuming, involving multiple steps, numerous tools, and extensive manual labor. However, {Company Name} has successfully challenged these limitations through their state-of-the-art forging process.The New Flange Forging Process:The newly developed process leverages advanced equipment, computer-aided design (CAD) software, and robotic automation to streamline the production of flanges. By eliminating tedious manual operations, this innovative method significantly reduces production time while ensuring precision and consistency throughout the manufacturing process.Key Features and Benefits:1. Enhanced Precision: The use of CAD software enables the creation of 3D digital models of flanges, ensuring accurate dimensions and reducing the risk of errors. This precision contributes to better performance, durability, and overall customer satisfaction.2. Time Efficiency: By applying automation and robotics, {Company Name} has dramatically reduced the time required for forging flanges. This process optimization translates into faster production cycles, allowing the company to meet market demands with greater agility.3. Cost Effectiveness: The cutting-edge technology employed in the flange forging process ensures minimal material waste, resulting in cost savings for {Company Name} as well as an environmentally friendly manufacturing approach.4. Quality Control: The company has implemented rigorous quality control measures at every stage of the process. This commitment to excellence guarantees consistently superior products, meeting international quality standards and regulations.Collaborative Efforts:To stay ahead in the competitive industry and ensure the success of this newest innovation, {Company Name} has partnered with renowned entities specializing in materials engineering and automation to create a synergy of expertise. This collaboration has enabled the company to harness their collective knowledge, resources, and expertise to refine the flange forging process continuously.Future Implications:The implementation of the advanced forging process by {Company Name} marks a significant stride in the manufacturing industry. The company's commitment to innovation, efficiency, and quality has far-reaching implications, not only within the flange manufacturing sector but also in inspiring similar advancements across various industrial domains.Conclusion:{Company Name}'s introduction of the breakthrough flange forging process is set to transform the manufacturing landscape. With its focus on precision, time efficiency, cost-effectiveness, and quality control, this innovative technique redefines industry standards and reaffirms the company's dedication to meeting market demands. As stakeholders around the world take note of this game-changing development, it serves as a testament to {Company Name}'s prominent position in the manufacturing sector.
Discover the Exquisite Art of Lost Wax Steel Casting for Superior Metal Craftsmanship
[Title]: Lost Wax Steel Casting: Revolutionizing the Manufacturing Industry[Subtitle]: Innovative Method Poised to Deliver Superior Products at Affordable Costs[Opening Paragraph]:The manufacturing industry is on the brink of a revolution with the emergence of Lost Wax Steel Casting (LWSC). This groundbreaking method is transforming the way steel products are manufactured by delivering superior quality and unmatched precision. Developed by industry leaders at {}, LWSC is set to establish new standards in the manufacturing sector, revolutionizing a wide range of industries and offering a cost-effective solution for businesses around the globe.[Company Introduction]:{}, a trailblazing manufacturing company founded by a team of experts, has pioneered the development of Lost Wax Steel Casting. With a mission to reshape the manufacturing landscape, they have honed this technique to perfection. Driven by innovation and a commitment to excellence, {} has quickly risen to become a dominant force in the industry. Their expertise, combined with the LWSC method, ensures that products manufactured by their company are of the highest quality, surpassing the standards imposed by traditional manufacturing techniques.[The Advantages of LWSC]:Lost Wax Steel Casting brings a multitude of advantages that are appealing to manufacturers across various sectors. Firstly, the method allows for intricate and complex designs to be replicated with utmost precision. By utilizing advanced technology and computer-aided design (CAD), {}, through their LWSC technique, can produce products with intricate details and unique shapes that were previously unattainable with conventional manufacturing processes.Secondly, LWSC guarantees excellent surface finishes and minimal post-production work. With the ability to create molds with extreme accuracy, {}, has eliminated the need for excessive grinding, polishing, or other additional finishing steps. This consequently reduces both production time and costs, allowing manufacturers to streamline their operations and bring products to market faster.Moreover, the process boasts exceptional material utilization, resulting in reduced waste and increased efficiency. By using the Lost Wax method, {} optimizes the utilization of raw materials, ensuring that every gram counts. This not only yields a more sustainable approach but also lowers manufacturing costs by reducing material waste, making it a desirable option for eco-conscious businesses.The versatility of the LWSC method is also a crucial factor that sets it apart. From small complex components to large industrial parts, the Lost Wax Casting technique can handle a wide range of sizes and shapes. Whether it is for the automotive industry, aerospace sector, or even artistic creations, LWSC proves its adaptability by meeting the diverse needs of various industries.[Positive Impact on Industries]:The introduction of Lost Wax Steel Casting is expected to have a transformative effect on numerous industries. For instance, in the automotive sector, the adoption of LWSC ensures the production of lightweight yet durable components, optimizing fuel efficiency while maintaining structural integrity. With concerns about carbon emissions and environmental impact at the forefront, Lost Wax Steel Casting provides an avenue for clean and sustainable manufacturing.In the aerospace industry, the precision and strength offered by LWSC make it ideal for creating critical components such as turbine blades. These intricate parts demand exceptional precision and durability, which traditional manufacturing methods have struggled to fulfill. However, Lost Wax Steel Casting provides a reliable solution, guaranteeing flawless components that meet stringent aerospace standards.Furthermore, the art and jewelry industry can also benefit immensely from the superior quality offered by LWSC. In artistic creations, the intricate details and delicate shapes can now be replicated flawlessly, allowing artists to bring their visions to life with precision. For jewelry manufacturing, the method offers increased design possibilities while maintaining a high level of durability.[Conclusion]:Lost Wax Steel Casting, developed by {} and rapidly gaining momentum in the manufacturing industry, is a game-changer that promises superior quality, reduced costs, and increased efficiency. {} continues to push the boundaries of innovation, challenging traditional manufacturing techniques and reshaping the industry's landscape. With its ability to deliver intricate designs, excellent surface finishes, and exceptional material utilization, LWSC is poised to revolutionize numerous sectors. As the world embraces this groundbreaking method, businesses are realizing the immense potential of Lost Wax Steel Casting, and its impact on the manufacturing industry is bound to be transformative.
High-Quality Forged Ball Valve: A Reliable Solution for Your Plumbing Needs
FORGING BALL VALVES: Ensuring Precision and Performance for Industrial ApplicationsIn today's rapidly advancing industrial landscape, companies are constantly seeking innovative solutions to bolster their operational efficiency and ensure the highest standards of performance. Among the critical components that enable smooth operations are forging ball valves, which play a vital role in controlling the flow of various fluids and gases. By combining advanced engineering techniques with cutting-edge materials, manufacturers are revolutionizing the quality and reliability of these valves, propelling industries into the future.Seeking to deliver these benefits to numerous industries, {Company Name}, a leading manufacturer of industrial valves, has introduced its state-of-the-art forging ball valves. With a reputation built on decades of engineering expertise and commitment to customer satisfaction, {Company Name} is dedicated to meeting the evolving needs of industries worldwide.Forging is a manufacturing process that involves shaping metal by applying compressive forces using hammers or presses. Compared to casting, forging enhances the mechanical properties of components, ensuring greater strength, durability, and resistance to external stress factors. By incorporating forging techniques into the production of ball valves, {Company Name} aims to provide superior performance and reliability, minimizing downtime and maximizing productivity for their customers.One of the key advantages of {Company Name}'s forging ball valves lies in their ability to withstand high-pressure environments. These valves are designed to efficiently regulate fluid and gas flow even under extreme operating conditions. This ensures uninterrupted operations for industries such as oil and gas, power generation, and petrochemicals, where pressure differentials can be substantial.Furthermore, {Company Name}'s forging ball valves offer exceptional resistance to corrosion, erosion, and wear and tear. Their robust construction and advanced material selection mitigate the risk of leakage or failure, improving the overall safety and reliability of industrial processes. By ensuring the integrity of fluid containment systems, these valves help protect employees, the environment, and valuable equipment.In addition to their superior performance, {Company Name}'s forging ball valves are engineered for ease of maintenance. The valves incorporate features that allow for quick and effortless disassembly and reassembly, which minimizes downtime during routine inspections or repairs. This results in increased operational efficiency and reduced maintenance costs for industries where uptime is critical.As a responsible industry player, {Company Name} also prioritizes environmental sustainability. The forging process employed in the manufacture of these valves reduces material waste compared to traditional casting methods, making it an environmentally friendly option. Furthermore, by prolonging the lifespan of equipment and preventing leaks or failures, {Company Name}'s forging ball valves contribute to the conservation of resources and the reduction of greenhouse gas emissions.{Company Name} continues to lead the forging ball valve industry through ongoing research and development. Its dedicated team of engineers constantly explores new materials, designs, and manufacturing techniques to enhance the performance and reliability of their valves. By closely collaborating with customers, {Company Name} ensures that its products are tailored to meet specific industry requirements and exceed expectations.In conclusion, {Company Name}'s forging ball valves offer a new standard of precision, performance, and reliability in the industrial sector. By leveraging the advantages of the forging process, these valves provide enhanced durability, resistance to high pressure and corrosion, and ease of maintenance, ultimately driving operational efficiency for a wide range of industries. As the company continues to innovate and collaborate, it remains at the forefront of forging ball valve technology, empowering industries worldwide to achieve excellence in their operations.
Top Auto Spare Parts That Will Keep Your Vehicle Running Smoothly
[Company Name] Revolutionizes Auto Spare Parts Industry with Cutting-Edge Innovations[City, Date] – In an industry where innovation often takes a backseat, [Company Name], an industry-leading provider of auto spare parts, has emerged as a game-changer, revolutionizing the way customers shop for and install automotive components. With its commitment to quality, reliability, and customer satisfaction, [Company Name] has quickly become a go-to destination for car owners and mechanics alike.Since its inception, [Company Name] has been on a relentless pursuit of perfection, pushing the boundaries of what is possible in the auto spare parts market. Through constant research and development, they have successfully developed a broad range of top-notch products that cater to the diverse needs of their customers.One of [Company Name]'s primary objectives is to ensure the utmost safety and durability of their products. With a team of experienced engineers and technicians, the company conducts rigorous tests on each component, guaranteeing that only the highest quality parts make their way onto the roads. This commitment to delivering superior products has earned [Company Name] a reputation for excellence and reliability.Moreover, [Company Name] understands that technological advancements have drastically changed the automotive landscape. To keep up with these changes, the company has invested heavily in research and development, resulting in innovative solutions that address the ever-evolving requirements of modern vehicles. Through their state-of-the-art manufacturing facilities, [Company Name] employs advanced production techniques and utilizes cutting-edge materials, ensuring that their parts not only meet but exceed industry standards.Customer convenience lies at the heart of [Company Name]'s business approach. Gone are the days where customers had to drive from one store to another, searching for the right spare parts. With their user-friendly online platform, customers can now browse their extensive catalog of auto spare parts from the comfort of their homes. The website features detailed product descriptions, high-resolution images, and compatibility information, allowing customers to make informed purchasing decisions.In addition to providing a seamless online shopping experience, [Company Name] has also invested in efficient logistics and supply chain management. With strategically located warehouses and a network of delivery partners, customers can expect prompt deliveries, minimizing downtime and maximizing convenience.Equally impressive is [Company Name]'s dedication to customer service. Their team of knowledgeable professionals is readily available to answer any queries, provide technical assistance, and offer expert advice. This level of personalized support ensures that customers receive the assistance they need, making their experience with [Company Name] truly exceptional.As an industry leader, [Company Name] actively promotes sustainability and environmental responsibility. The company recognizes its role in reducing its carbon footprint and has implemented numerous initiatives to minimize its impact on the environment. From utilizing eco-friendly packaging materials to adopting energy-efficient manufacturing processes, [Company Name] is committed to creating a greener and more sustainable future.Looking ahead, [Company Name] has ambitious plans to further innovate and expand its product offerings. Their dedicated team is continuously researching emerging technologies, exploring new market trends, and identifying opportunities to provide customers with even more advanced solutions. With their relentless drive for improvement, [Company Name] aims to set new benchmarks in the auto spare parts industry.The automotive industry has long awaited a company that embodies excellence, reliability, superior technology, and a customer-centric approach. With [Company Name]'s unwavering commitment to all these aspects, they have emerged as a force to be reckoned with, setting the stage for a new era in the auto spare parts industry.
Top Techniques for Efficient Aluminum Casting Process Unveiled
Title: Pioneering Aluminum Casting: Revolutionizing the Manufacturing IndustryIntroduction:In an era driven by technological advancements, the manufacturing industry is witnessing a groundbreaking innovation: Aluminum Casting. The technique of casting aluminum has caught the attention of various industries owing to its strength, flexibility, and cost-effectiveness. In this news piece, we explore how one company, with its expertise in Aluminum Casting, is transforming the manufacturing landscape.Company Introduction: [Remove brand name]The company at the forefront of this aluminum casting revolution is a leading manufacturer with unparalleled expertise in the field. Their extensive experience and dedication to excellence have earned them a prominent position within the manufacturing industry. Committed to delivering outstanding results, this company has developed state-of-the-art facilities, advanced equipment, and a team of highly skilled professionals who share a passion for innovation.Breaking Down Aluminum Casting:Aluminum casting is a process that involves making three-dimensional objects by pouring molten aluminum into a mold, enabling the creation of complex and intricately designed components. The versatility of this method allows manufacturers to produce parts of different shapes, sizes, and designs, catering to various industries such as automotive, aerospace, construction, and electronics.Revolutionizing Manufacturing Processes:1. Lightweight Advantages:One significant advantage of aluminum casting lies in the lightweight nature of the material itself. As a result, industries such as automotive and aerospace are increasingly opting for aluminum components over traditional materials like steel. The reduction in weight contributes not only to improved fuel efficiency but also to enhanced performance and maneuverability of vehicles. Moreover, lightweight aluminum components reduce the overall carbon footprint, promoting sustainability within the industry.2. Strength and Durability:Aluminum casting offers exceptional strength and durability. The unique characteristics of aluminum make it an ideal choice for parts subjected to high stress, heat, or corrosive environments. This advantage translates into longer lifespan, minimized maintenance costs, and increased reliability of the final products.3. Cost-Effective Solutions:By utilizing aluminum casting, manufacturers can achieve significant cost savings. Aluminum, being abundant and readily available, is a cost-effective material option compared to other metals. The simplicity of the casting process also contributes to reduced production time and cost, making it an economically viable solution for a wide range of industries.4. Design Freedom:Aluminum casting provides designers with unmatched freedom to create intricate and complex shapes. The molten aluminum can be easily customized and cast into various molds, allowing manufacturers to meet their clients' specific requirements with ease. This advantage enables the production of highly customized components that enhance product aesthetics and functionality.Conclusion:The advent of aluminum casting has undoubtedly revolutionized the manufacturing industry, offering numerous benefits such as lightweight construction, superior strength, cost-effectiveness, and design freedom. As companies continue to harness the potential of this technique, we can expect to witness groundbreaking advancements in various sectors. With its extensive expertise, state-of-the-art facilities, and dedicated team, the company stands at the forefront of this aluminum casting revolution, paving the way for a future driven by innovation, reliability, and sustainability in manufacturing.
Benefits of Aluminium Casting Parts for your Manufacturing Needs
[Title]: Leading Manufacturer Introduces High-Quality Aluminium Casting Parts for Diverse Industries[Subtitle]: Emphasizing Quality, Durability, and Innovation, [Company Name] Offers an Extensive Range of Aluminium Casting Parts to Cater to Global Markets[date][City], [State] - [Company Name], a renowned global leader in the manufacturing industry, sets a new benchmark in the market with its exceptional range of high-quality aluminium casting parts. Catering to diverse industries, the company leverages its state-of-the-art facilities and cutting-edge technology to produce reliable and durable components that meet the evolving needs of its customers.[Company Name] prides itself on its unwavering commitment to quality. With decades of industry expertise, the company consistently strives to deliver precision-engineered casting parts that exceed customer expectations. The aluminium casting parts offered by [Company Name] are widely recognized for their superior performance, reliability, and impeccable finish.Unparalleled durability is a distinguishing feature of [Company Name]'s aluminium casting parts. Using advanced production techniques and employing a team of highly skilled engineers and technicians, the company ensures that each component withstands extreme conditions, guaranteeing longevity and robustness. Whether it's in the automotive, aerospace, energy, or any other industry, [Company Name]'s aluminium casting parts demonstrate exceptional durability in demanding applications.Furthermore, [Company Name]'s commitment to innovation ensures that it stays at the forefront of the industry. By continuously investing in research and development, the company pioneers cutting-edge casting techniques and materials, providing customers with access to the latest advancements. This dedication to innovation has allowed [Company Name] to develop casting parts that boast unmatched precision and efficiency, enabling its customers to gain a competitive edge in the market.The versatile product range offered by [Company Name] caters to a wide array of industrial applications. From intricate automotive components such as engine blocks, transmission cases, and cylinder heads, to aerospace parts like turbine blades and structural components, [Company Name] provides tailored solutions that meet the unique requirements of its clients. Moreover, the company's aluminium casting parts have gained prominence in the energy sector, powering critical infrastructure and contributing to sustainable energy solutions.[Company Name]'s commitment to sustainable practices is reflected in its manufacturing processes. The company adheres to strict environmental standards, minimizing its carbon footprint and promoting a circular economy. By employing recyclable materials and optimizing energy consumption, [Company Name] ensures that its aluminium casting parts contribute to a greener and more sustainable world.Proudly serving a global clientele, [Company Name] has established an extensive distribution network that spans across multiple continents. The company's commitment to customer satisfaction is evident in its reliable supply chain and efficient logistics, guaranteeing on-time delivery to every corner of the globe. With a strong focus on customer support and after-sales service, [Company Name] nurtures long-lasting relationships with its clients, ensuring their success and satisfaction.As the demand for high-quality aluminium casting parts continues to grow, [Company Name] remains steadfast in its pursuit of excellence. By harnessing technological advancements and embracing industry best practices, the company seeks to expand its offerings, delivering even greater value to its customers around the world.About [Company Name]:[Company Name] is a leading manufacturer of high-quality aluminium casting parts for diverse industries. With a strong emphasis on quality, durability, and innovation, the company aims to provide reliable components that surpass industry standards. Through its commitment to sustainability and customer satisfaction, [Company Name] has established itself as a trusted partner for businesses worldwide.For more information, please visit [website].[END]
Top Car Parts: Essential Components for Efficient Vehicle Performance
Title: Leading Automotive Supplier Car Parts Unveils Innovative Solutions for Better Vehicle PerformanceIntroduction:Car Parts is a renowned automotive supplier with a strong reputation for providing high-quality components to the global automotive industry. With a commitment to innovation and continuous improvement, Car Parts has announced its latest range of ground-breaking solutions designed to enhance vehicle performance and deliver an exceptional driving experience. In this news article, we will explore the company's new offerings and how they are set to revolutionize the automotive industry.Paragraph 1: Car Parts has introduced an array of cutting-edge products that aim to improve vehicle performance, safety, and efficiency. These state-of-the-art components have been meticulously designed and thoroughly tested to meet the demanding needs of the modern automotive industry. With a dedicated team of experts, Car Parts focuses on addressing critical challenges in the sector, such as reducing emissions, increasing fuel efficiency, and enhancing durability.Paragraph 2: One of the highlights of Car Parts' latest offerings is the revolutionary Engine Enhancement Module (EEM). This groundbreaking technology enables vehicles to achieve optimal engine performance while simultaneously reducing environmental impact. By seamlessly integrating with the vehicle's existing engine control unit, the EEM optimizes fuel injection, ignition timing, and air-fuel ratio, resulting in improved power, efficiency, and reduced emissions. Car Parts' EEM represents a significant milestone in the pursuit of sustainable transportation.Paragraph 3: In addition to the EEM, Car Parts recognizes the importance of safety in the automotive industry. The company is proud to introduce its Advanced Driver Assistance Systems (ADAS), designed to enhance vehicle safety and reduce the risk of accidents. Car Parts' ADAS utilizes state-of-the-art sensors and cutting-edge algorithms to enable features such as blind-spot detection, lane departure warnings, and adaptive cruise control. These intelligent systems work together harmoniously to provide drivers with an extra layer of protection, ensuring a safer driving experience for all.Paragraph 4: Car Parts' commitment to innovation doesn't stop at engines and safety. The company has also unveiled a range of lightweight materials and components that significantly contribute to improving overall vehicle efficiency. By employing advanced engineering techniques and utilizing materials such as carbon fiber, Car Parts' lightweight solutions reduce the weight of vehicles without compromising strength or safety. This results in improved fuel economy, reduced emissions, and enhanced agility.Paragraph 5: To meet the diverse needs of their global clientele, Car Parts maintains an extensive network of manufacturing facilities across several regions. These strategically located facilities enable Car Parts to efficiently meet customer demands while ensuring the highest standards of quality and reliability. With an unwavering commitment to customer satisfaction, the company also offers exceptional after-sales service, ensuring a seamless ownership experience for their clients worldwide.Conclusion:Car Parts' groundbreaking solutions have set a new benchmark in the automotive industry. With their focus on enhancing vehicle performance, safety, and environmental sustainability, the company is poised to drive the automotive industry forward. By consistently pushing the boundaries of innovation and delivering top-notch products and services, Car Parts continues to establish itself as a leading automotive supplier globally. As the industry embraces technological advancements, Car Parts remains at the forefront, revolutionizing the future of automotive excellence.
Unveiling the Intricate Process of Forging: An In-Depth Look
Title: Innovations in the Process of Forging Revolutionize Manufacturing IndustryIntroduction:The process of forging, a centuries-old technique of shaping metal, has undergone a transformation thanks to groundbreaking innovations introduced by several industry leaders. In particular, companies like {} have played a pivotal role in revolutionizing the manufacturing sector through their cutting-edge technologies and techniques. This article discusses how these advancements have improved the forging process, leading to enhanced product quality, increased production efficiency, and higher customer satisfaction.Body:1. The Foundations of Forging:Forging is the process of shaping metal through the application of tremendous pressure, usually with the help of hydraulic or mechanical force. Known for its strength, durability, and reliability, forged components find applications in various industries, including automotive, aerospace, defense, and construction. Traditionally, forging was a labor-intensive process that required skilled craftsmen to manually shape the metal into the desired form. However, with the advent of modern technologies, the forging industry has witnessed significant advancements, which have simplified and optimized the manufacturing process.2. Introduction of Advanced Materials:One key innovation lies in the utilization of advanced materials for forging applications. With the development of high-strength alloys, superalloys, and composite materials, manufacturers now have access to materials with enhanced characteristics, such as superior mechanical properties, heat resistance, and corrosion resistance. By utilizing these advanced materials, companies have been able to produce components that are not only lighter and more durable but also better suited for specific operational conditions.3. Computer-Aided Design and Manufacturing (CAD/CAM) Integration:Integration of computer-aided design and manufacturing (CAD/CAM) systems has been instrumental in streamlining the entire forging process. By digitizing the design, simulation, and manufacturing phases, engineers can now create intricate component geometries with enhanced precision and accuracy. CAD/CAM integration allows for the optimization of tooling and die designs, reducing material waste and production costs while improving overall product quality.4. Automation and Robotics:The introduction of automation and robotics in forging facilities has led to a significant boost in production efficiency and consistency. Intelligent robotic systems can now handle complex tasks previously performed by human operators, such as loading and unloading parts, transferring components between workstations, and performing quality inspections. This integration of automation not only improves productivity and reduces labor costs but also ensures a higher level of precision, repeatability, and safety throughout the manufacturing process.5. Simulation and Predictive Analysis:Simulations and predictive analysis tools are transforming the way manufacturers approach the forging process. Advanced software can simulate the behavior of metals under extreme heat and pressure, accurately predicting how they will deform, crack, or fail. By simulating different scenarios, engineers can optimize the process parameters, tooling designs, and material selection, reducing the time and costs associated with physical prototyping and testing. This technological advancement allows for faster development cycles, improved component quality, and increased overall efficiency.6. Additive Manufacturing in Forging:Additive manufacturing, often referred to as 3D printing, has also found its way into the realm of forging. Through the utilization of metal powders and advanced printing techniques, complex components can be fabricated layer by layer, eliminating the need for traditional forging processes. This disruptive technology offers increased design flexibility, reduced material waste, and shorter production times, enabling manufacturers to create intricate and lightweight components that were previously unattainable.7. Quality Assurance and Traceability:In addition to process improvements, modern forging techniques have also enhanced quality assurance and traceability. Manufacturers now employ advanced inspection technologies, such as non-destructive testing and optical measurement systems, to ensure that components meet the highest industry standards. Additionally, blockchain-based systems facilitate real-time traceability, providing customers with transparent information about the origin, production, and testing of forged components. These advancements instill confidence in the quality and reliability of the products while meeting the rigorous demands of various regulatory bodies.Conclusion:The evolution of the forging process, driven by the innovative technologies introduced by companies such as {}, has ushered in a new era of manufacturing excellence. From advanced materials and CAD/CAM integration to automation, simulation, and additive manufacturing, these advancements have significantly improved product quality, production efficiency, and customer satisfaction. The future of forging appears promising, with continued research and development propelling the industry towards greater innovation and success.